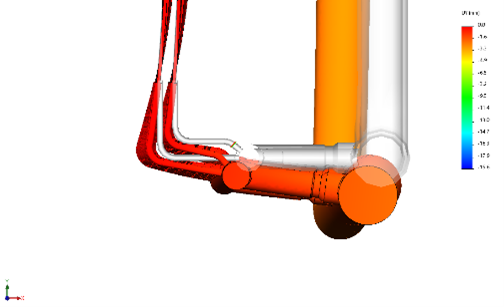
Life Assessments
Knowing the remaining useful operating life of your boiler, HRSG and associated balance-of-plant is a key parameter for effective management of your thermal power plant.
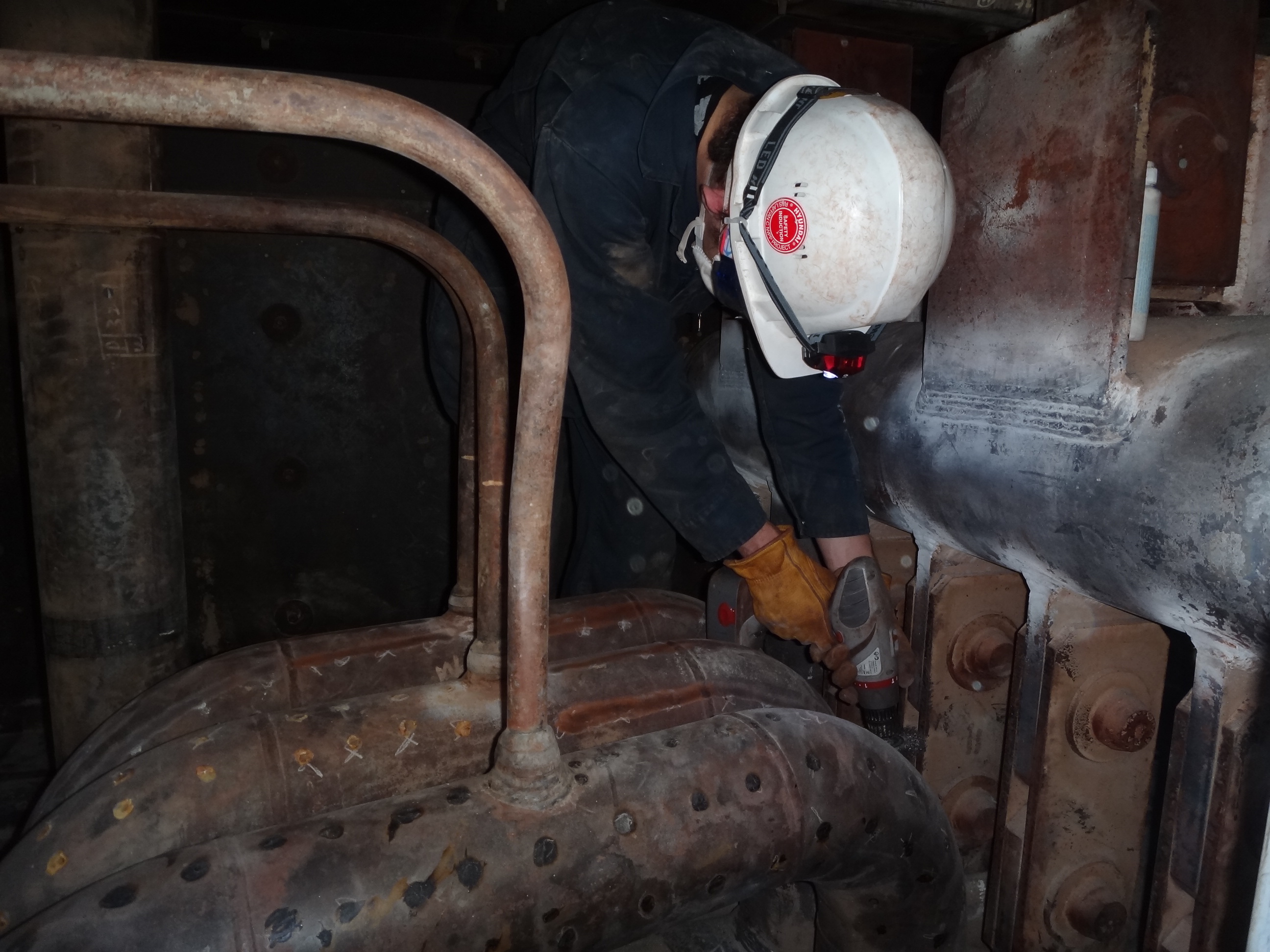
Optimized NDE
Risk-based inspection (RBI) is an approach for ranking the priority of inspection and maintenance according to an assessed risk to the component or system integrity. One key aspect of any RBI program is to carefully select the locations for non-destructive examination (NDE) that are most susceptible to damage, according to the component's design and past and project operating mode, while considering the resources and time available during an upcoming inspection. Using multi-disciplinary experience and tools (thermal simulation, life assessment, structural calculations….) Tetra will help you get the most out of your NDE campaigns, by providing pre-outage planning, on-site supervision and post-inspection review.
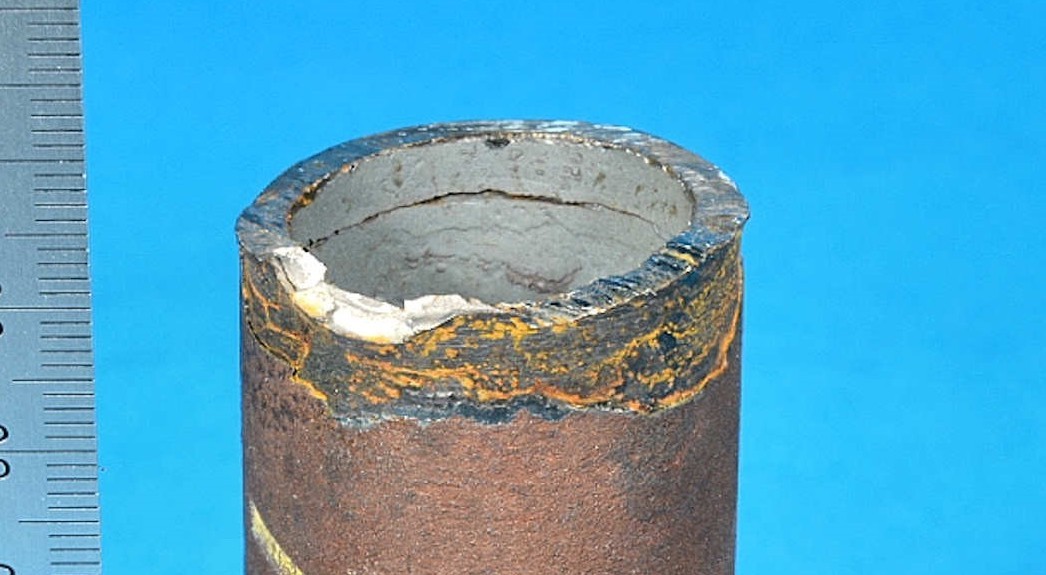
Root Cause of Failure (RCA)
Knowing the fundamental causes leading to failure is essential to mitigate the risk of the failure repeating. Tetra Engineering calls on an interdisciplinary team to assess the failure (or degradation) and determine the root cause.
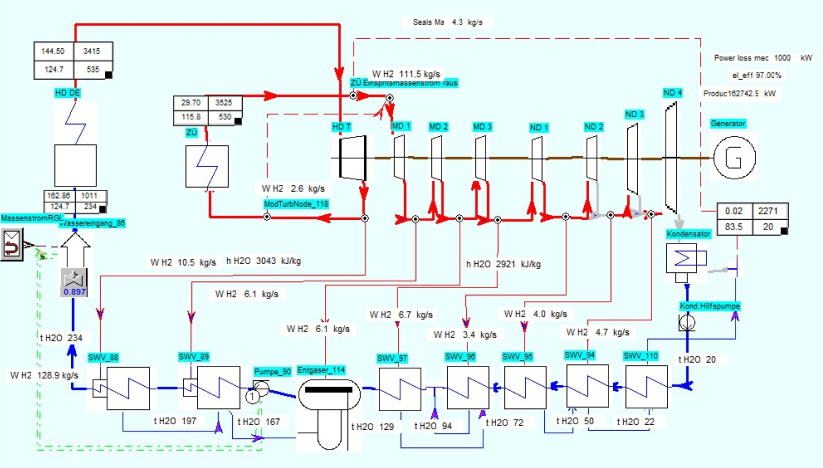
Performance & Efficiency Assessments
Services to help you evaluate how your operating performance has changed since the plant / boiler was commissioning, or to help you check the potential performance impact of planned modifications before they are implemented.
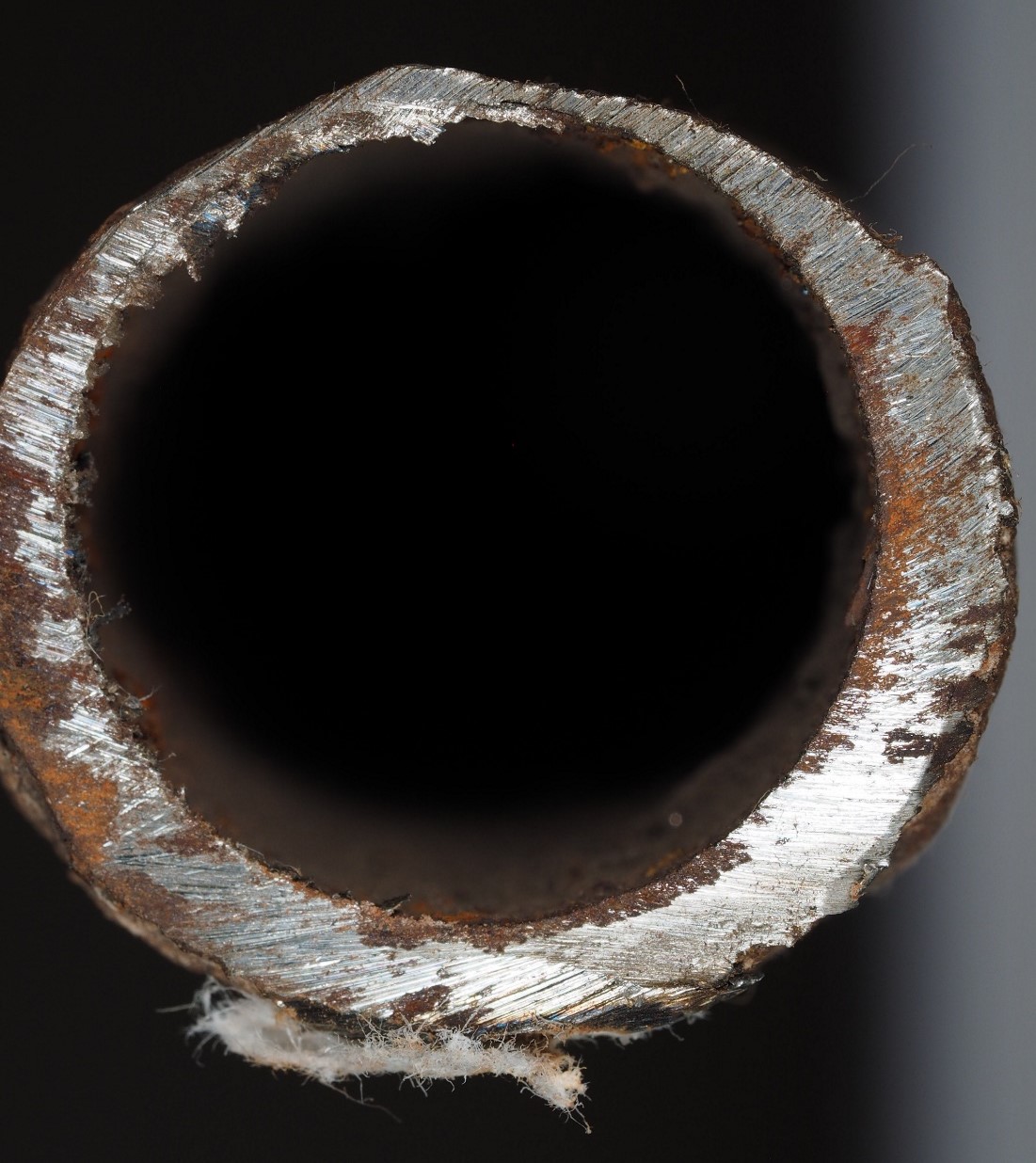
Fitness for Service
A fitness for service (FFS) evaluation is a process for assessing the structural integrity and safety of components that may have experienced damage and deterioration during their service life.
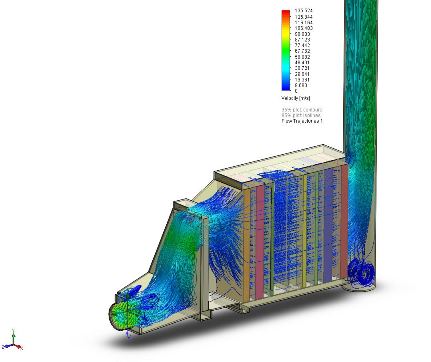
Boiler Process Modelling and Simulation
Tetra Engineering provides a full-scope service for the modelling and operation analysis of all types of natural or forced circulation Power Boiler and HRSGs, including supercritical and once-through designs. This can be integrated into a full plant model to incorporate the steam turbine and steam cycle balance of plant.
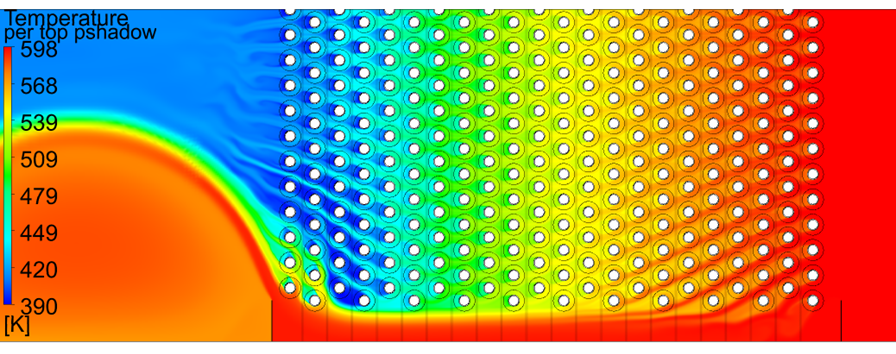
Flow Accelerated Corrosion Assessment (FAC)
Identify and prevent tube and pipe thinning caused by flow-accelerated corrosion (FAC) to avoid ruptures and leaks.